Wool production traditionally has been one of Wales' most important industries. At its height, it's said there were well over 300 active woolen mills located across the country (an area about the size of New Jersey). By the mid-twentieth century, however, this number had drastically declined, due to a combination of newer technologies, changing fashions, and competition with the mills of northern England and other markets. By 2013, there were just nine commercial woolen mills still in operation, most family-owned operations, producing traditional Welsh cloth on old looms. One of these is Trefriw Woolen Mills in the village of Trefriw, Conwy, in northern Wales.
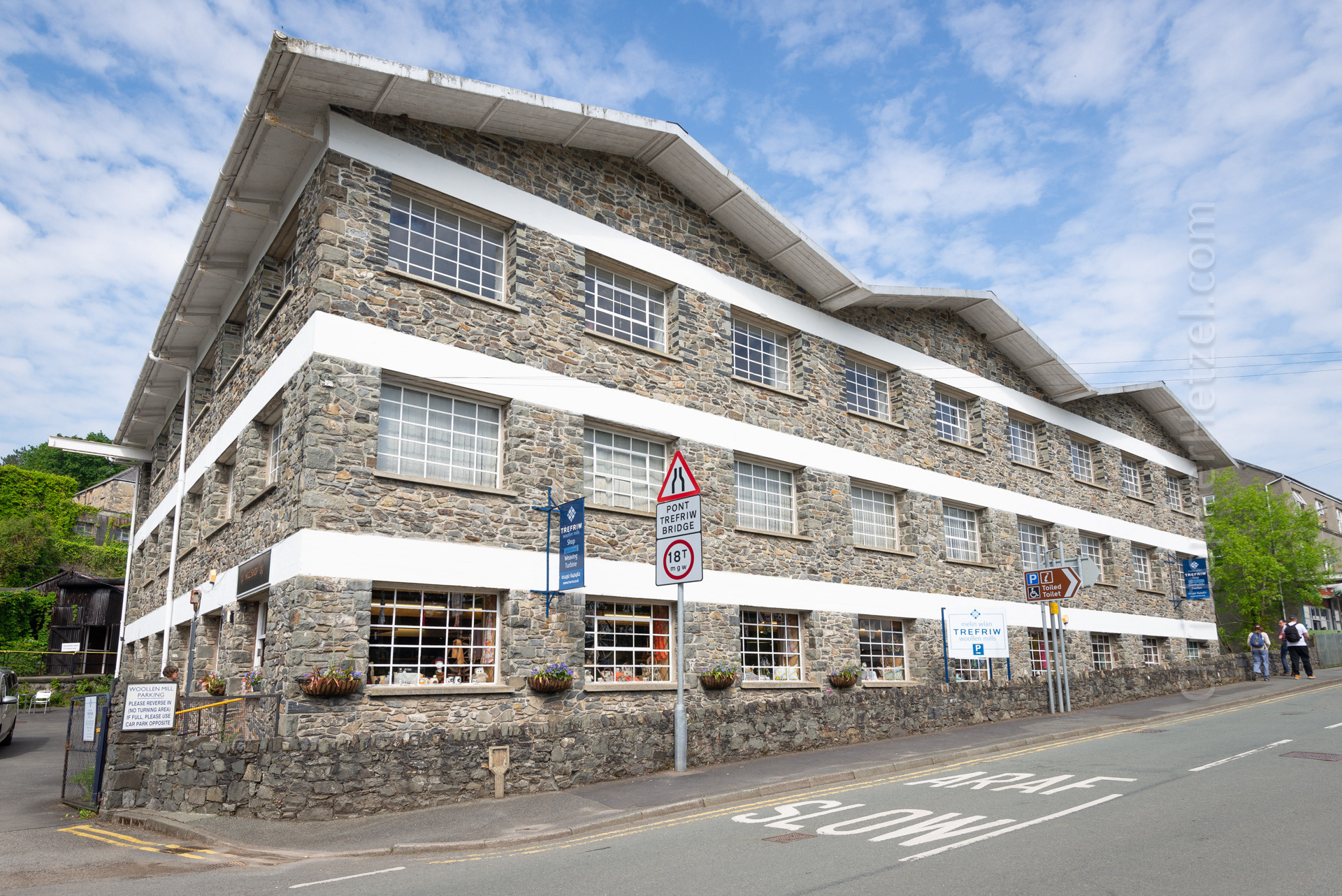
Trefriw Woollen Mills has been in operation at its present location since the 1820s on the bank of the River Crafnant, a tributary of the River Conwy, which is the main river of the Conwy valley in northwest Wales. Originally called the Vale of Conwy Woollen Mill, it was initially a 'Pandy' or 'Fulling mill,' which washed and finished already woven cloth from individual home-cottage weavers. The mill was purchased by Thomas Williams in 1859 and expanded into a full commercial operation, leading into the industrial revolution. Woolen goods produced by the mill were taken to ports on Wales' north coast via the River Conwy, where they were then exported to various markets.
The mill's original 36-foot overshot waterwheel was dismantled and replaced by a hydroelectric turbine in 1900. This, too, was subsequently replaced by the facility's two existing Pelton hydro-electric wheel turbines in 1942 and 1951. These turbines deliver 60 kW of electricity to power the mill's machinery, most of which was acquired in the 1950s and 1960s. The main building that exists today, with its three shallow-sloping roofs, was erected around 1970. It houses the mill's retail outlet and two floors of machinery - for carding, spinning, twisting, warping, weaving and packaging. Several older mill structures remain behind the main building, accessible from the mill yard, including the blending and willowing sheds.
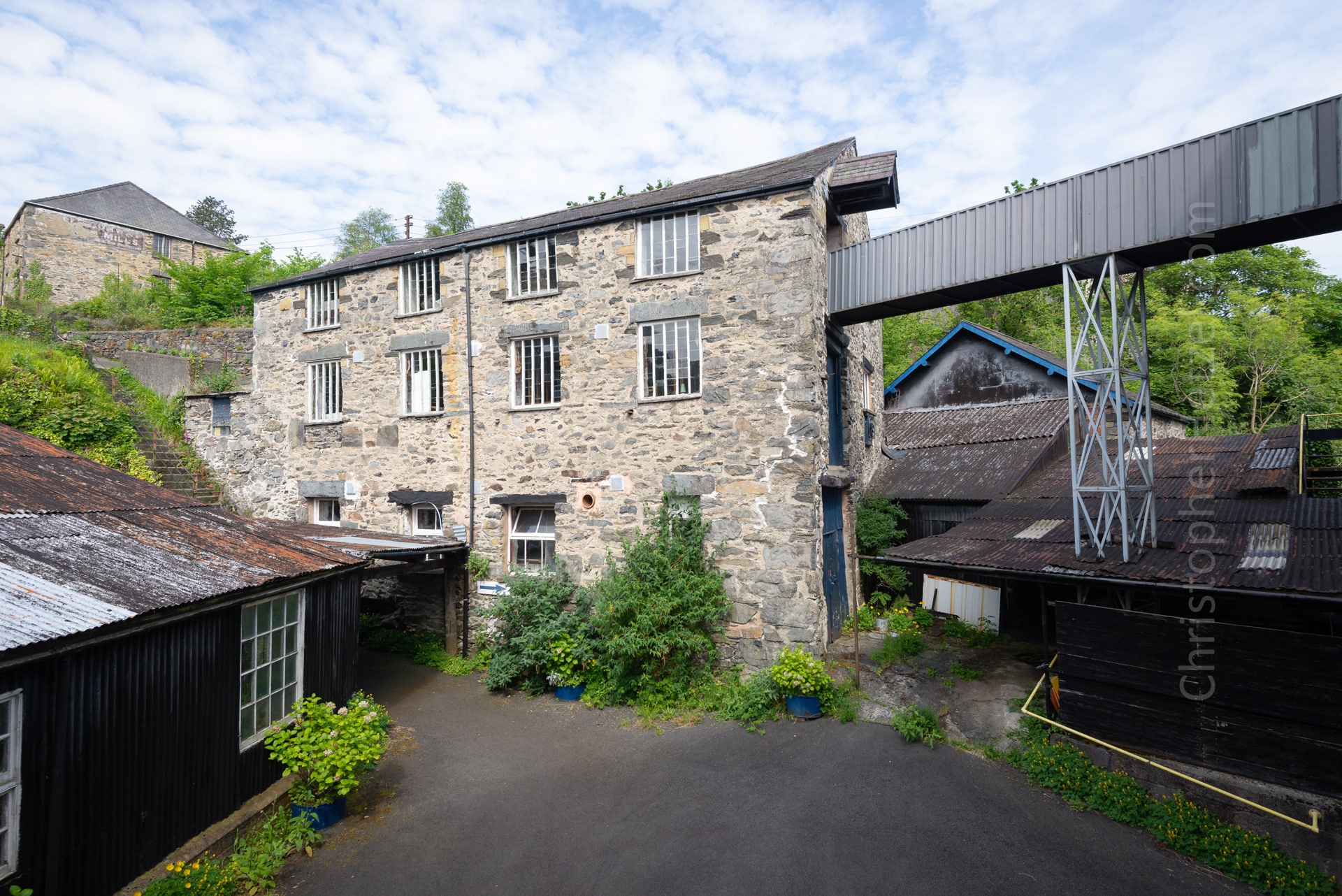
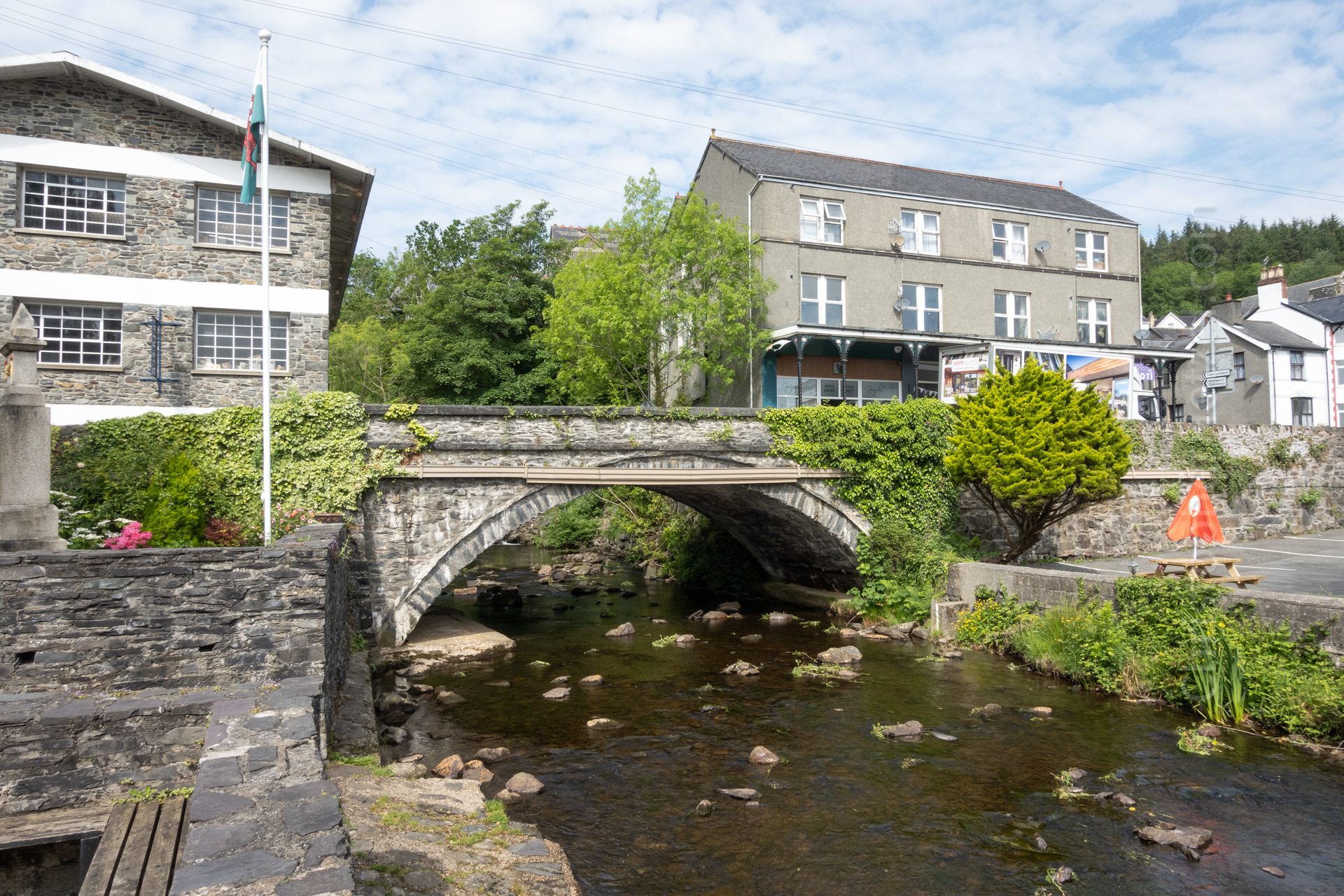
The River Crafnant. The mill is on the left.
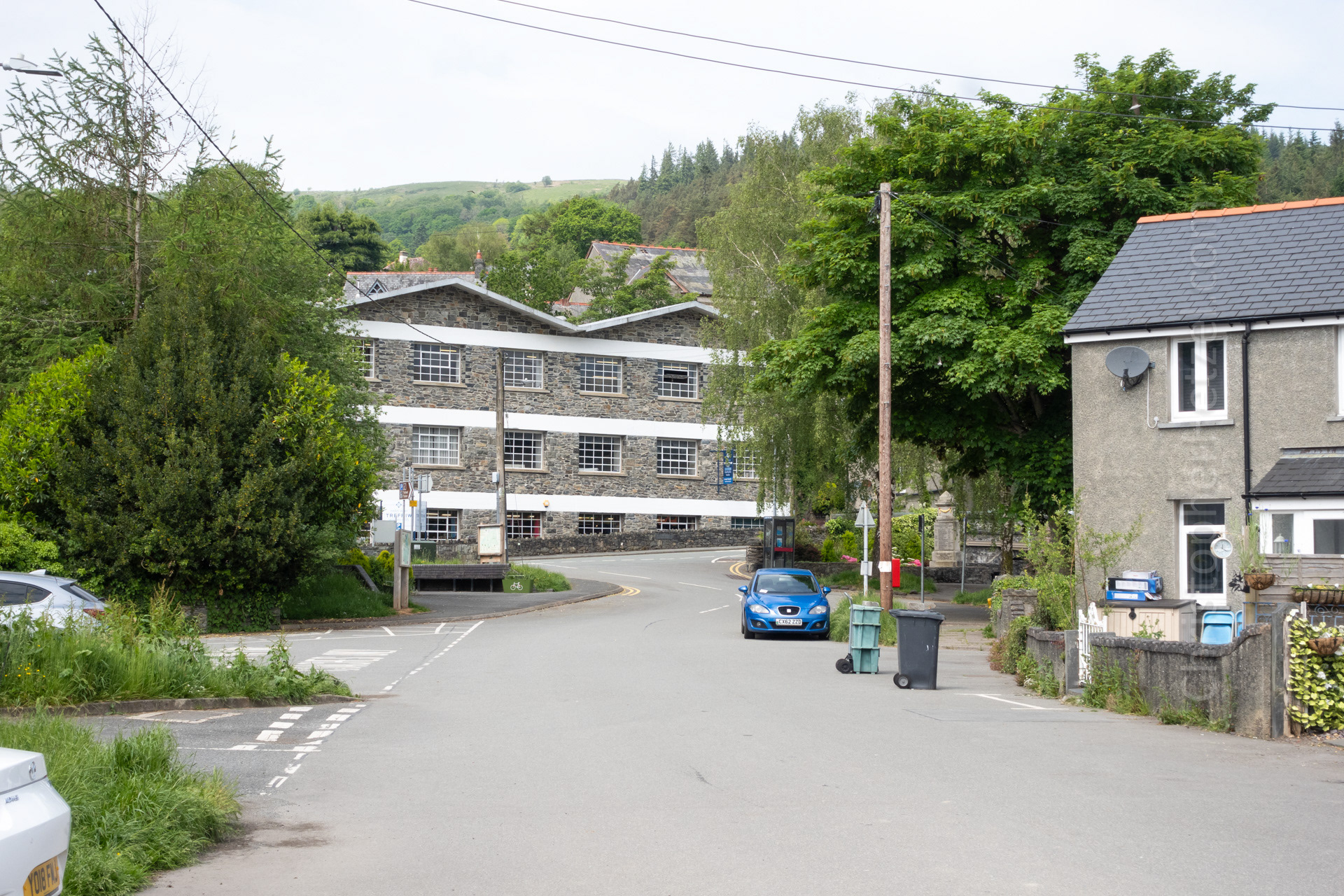
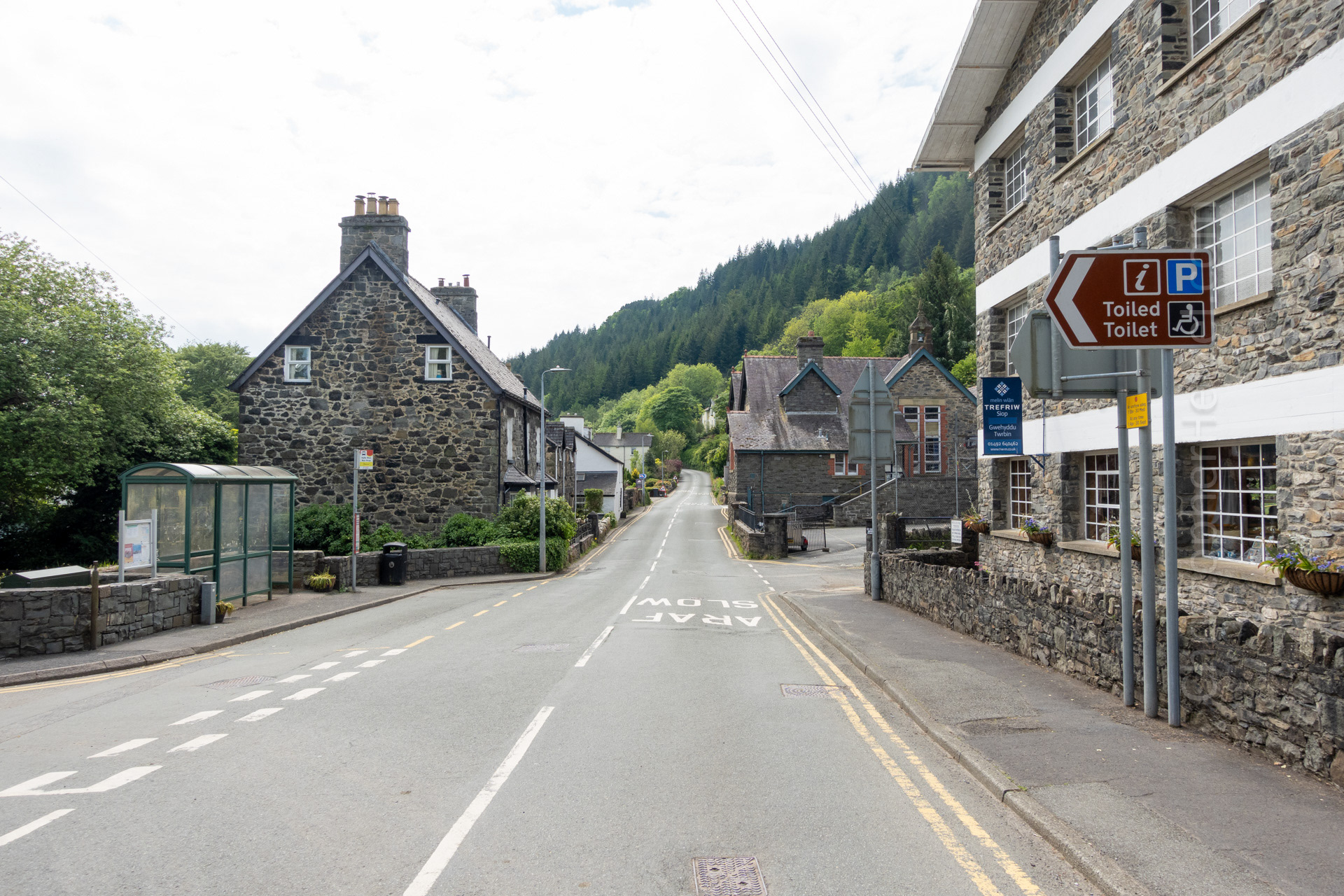
The main street of Trefriw village.
Weaving (above) - The weaving of cloth is done by a loom, which utilizes as many as five shuttles to carry the weft thread horizontally across the vertical warp, while the shafts are raised and lowered to make the pattern. This video shows the operator replacing the bobbin in one of the shuttles with new yarn.
Warping (below - left) - To prepare for weaving, threads of yarn are transferred from cones to bobbins, which fit into the shuttles of the weaving machines. Meanwhile, a warping machine arranges the threads to form the warp. This video shows the former process. The cones are on the left, the bobbins sit horizontally on the right.
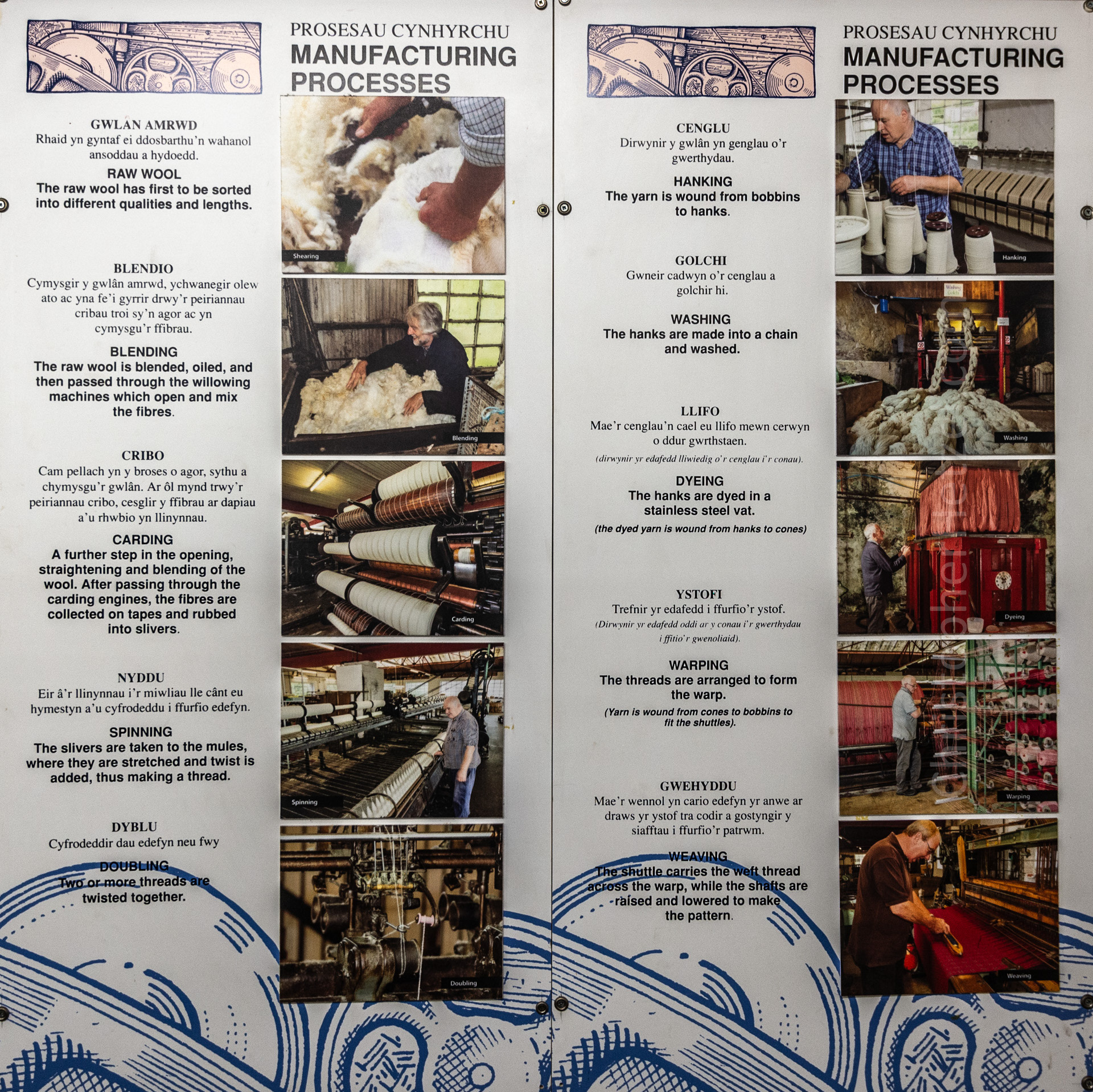
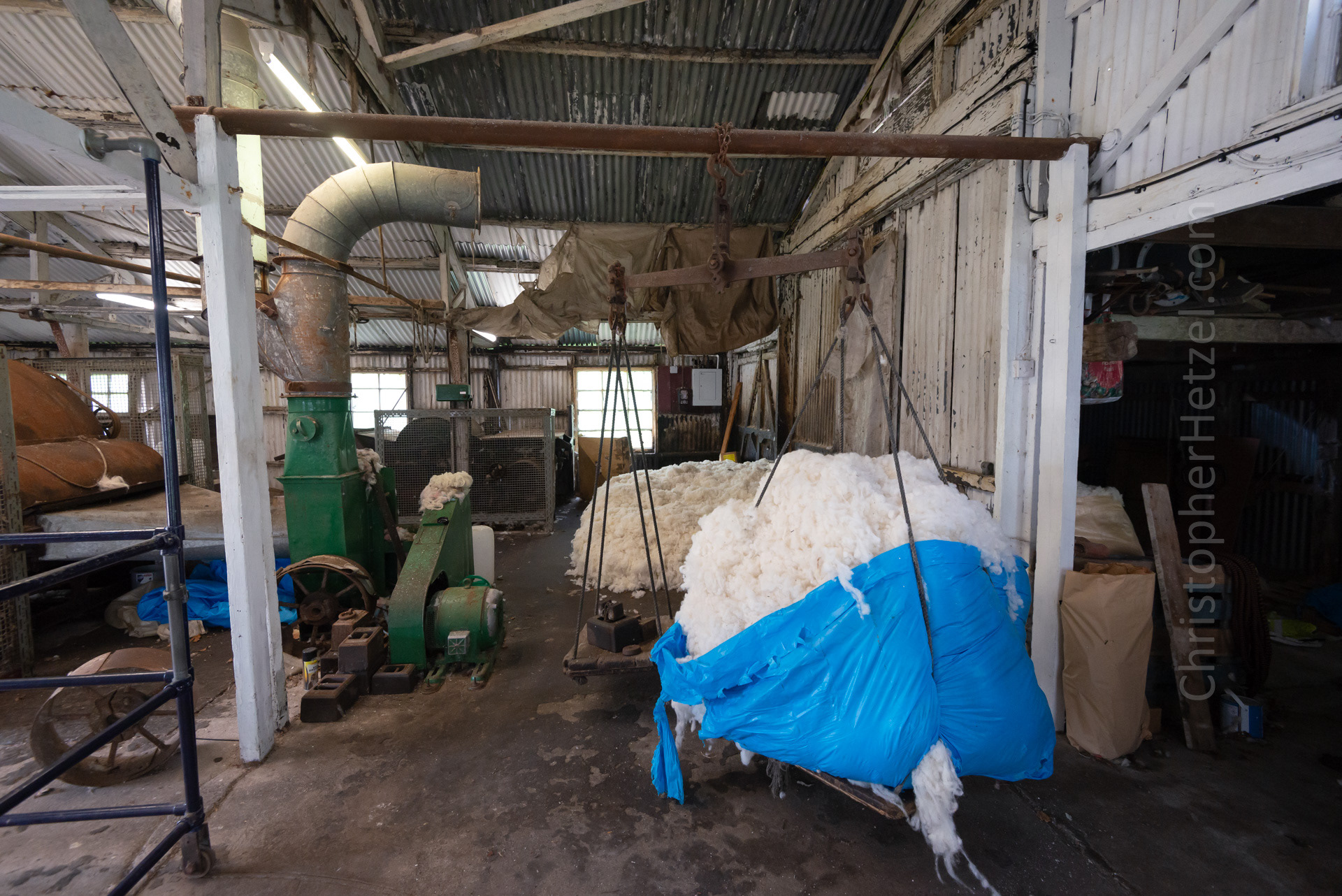
Blending - In the blending shed, the raw wool is blended, oild, and then passed through willowing machines, which open and mix the fibers.
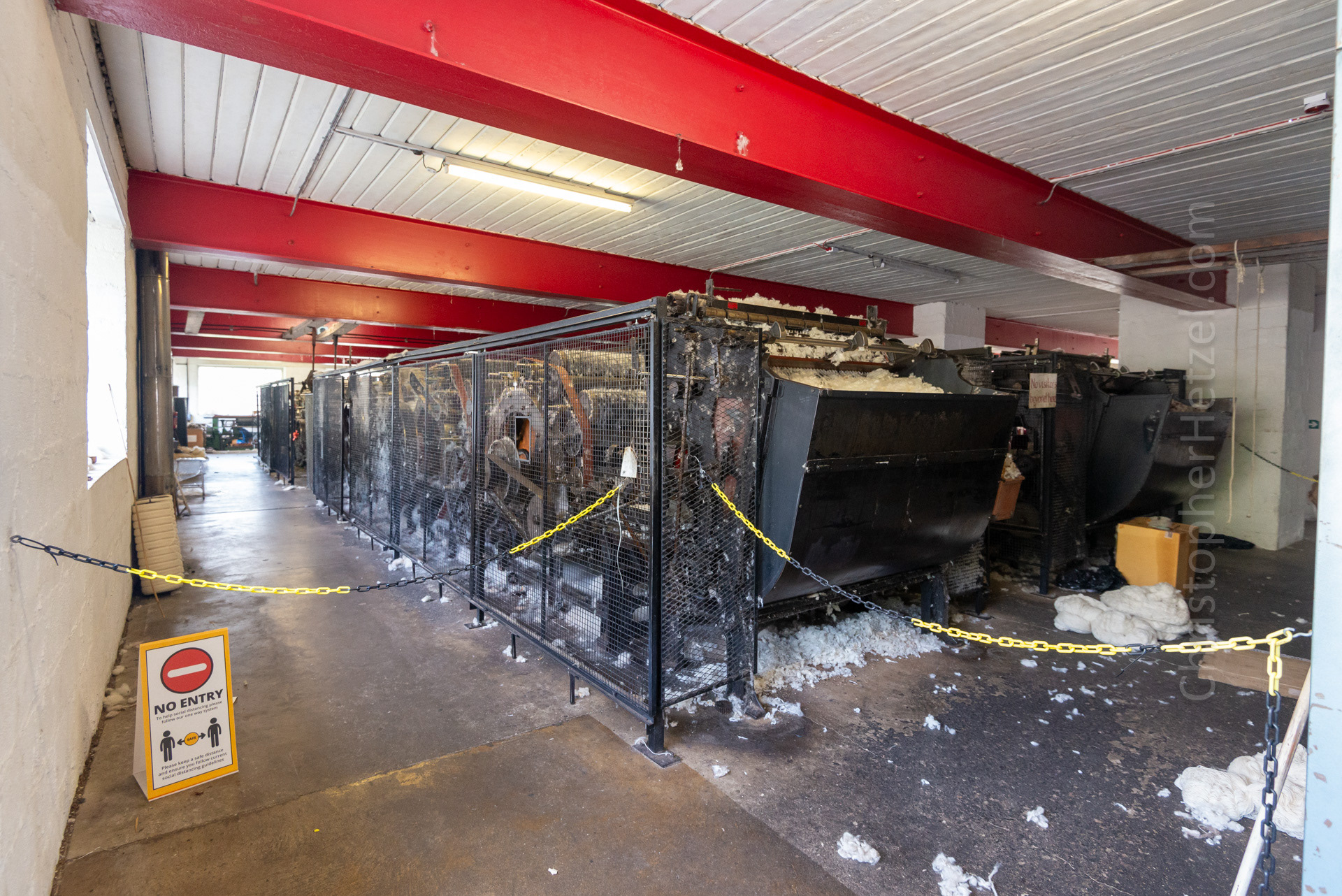
Carding - A further step in the opening, straightening and blending of the wool, the wool is passed through carding engines, which collects the fibers on 'tapes' and rubs them into 'slivers.'
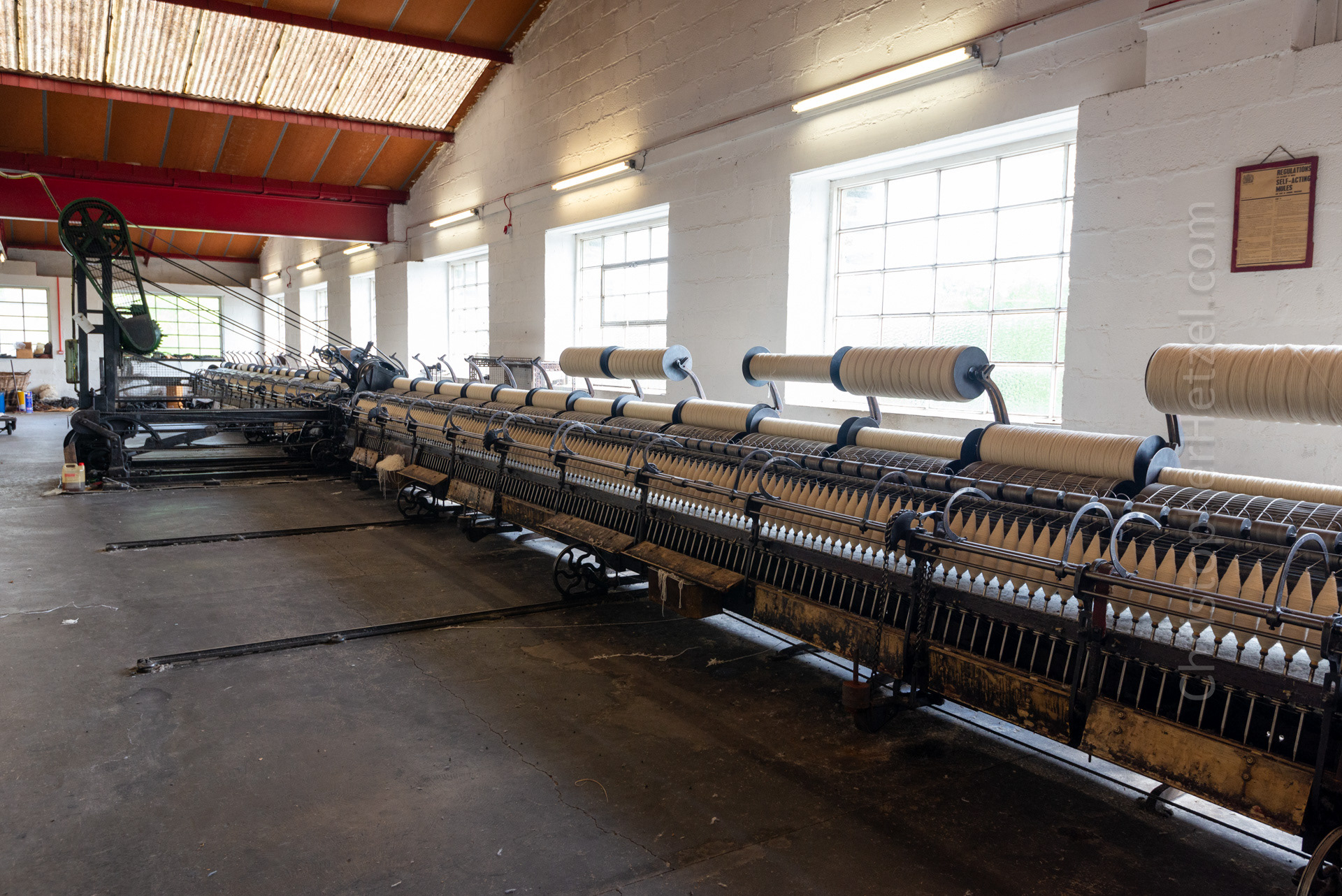
Spinning - After being carded, the 'slivers' are spun on the spinning mules, where they are stretched and twist is added, thus making thread.
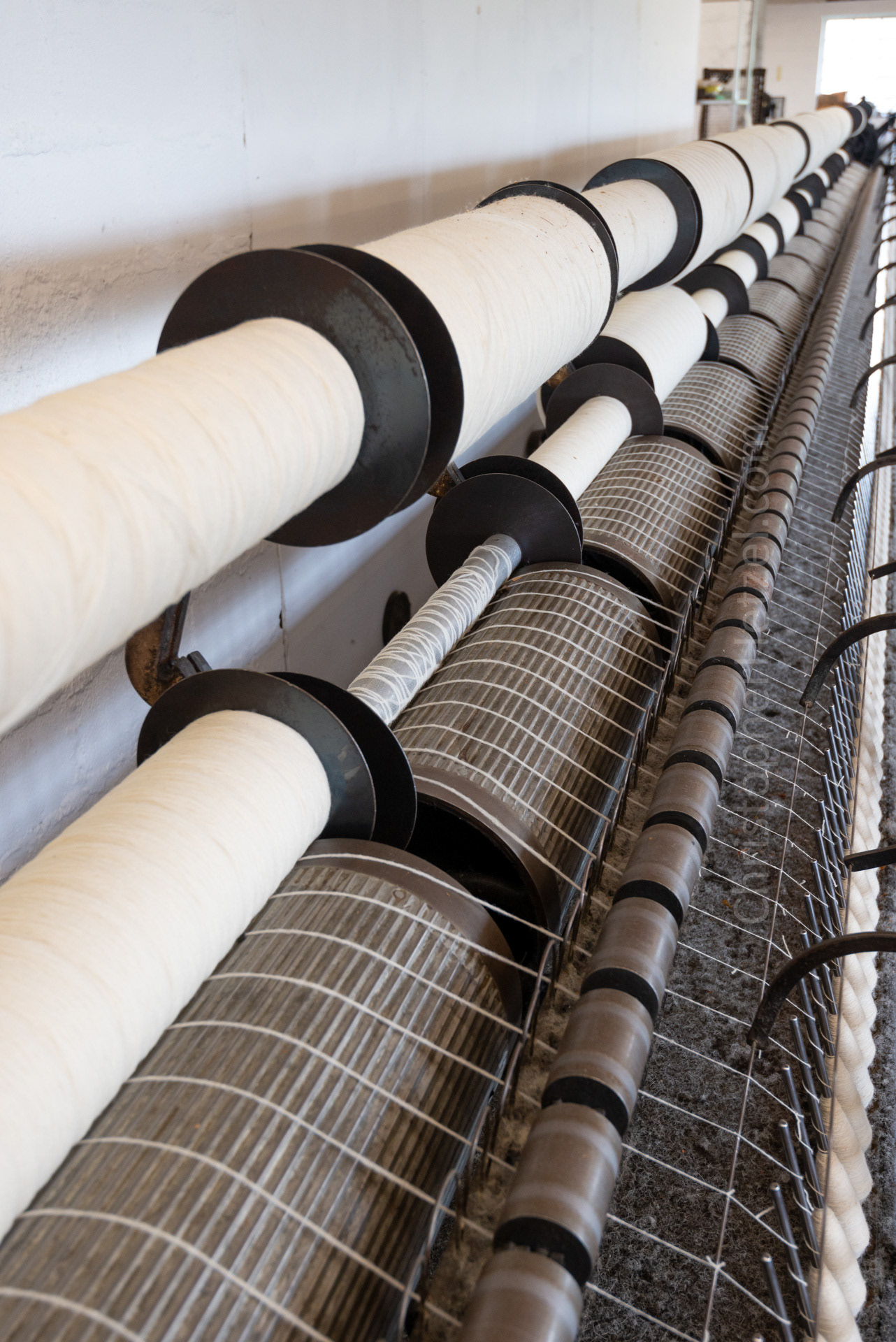
Spinning - After being carded, the 'slivers' are spun on the spinning mules, where they are stretched and twist is added, thus making thread.
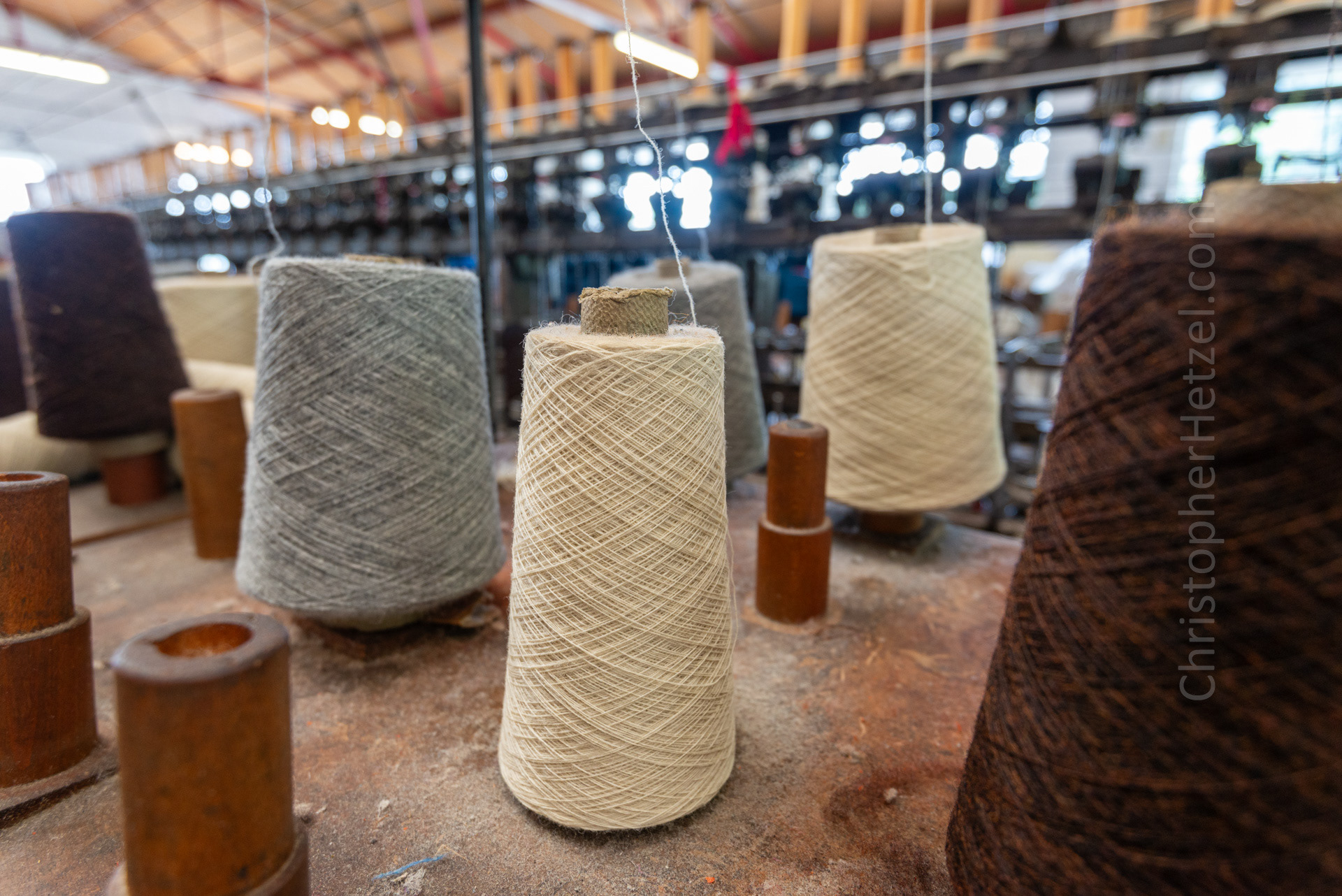
Hanking - The yarn is would from bobbins to 'hanks,' which is the form used to wash and dye the yarn.
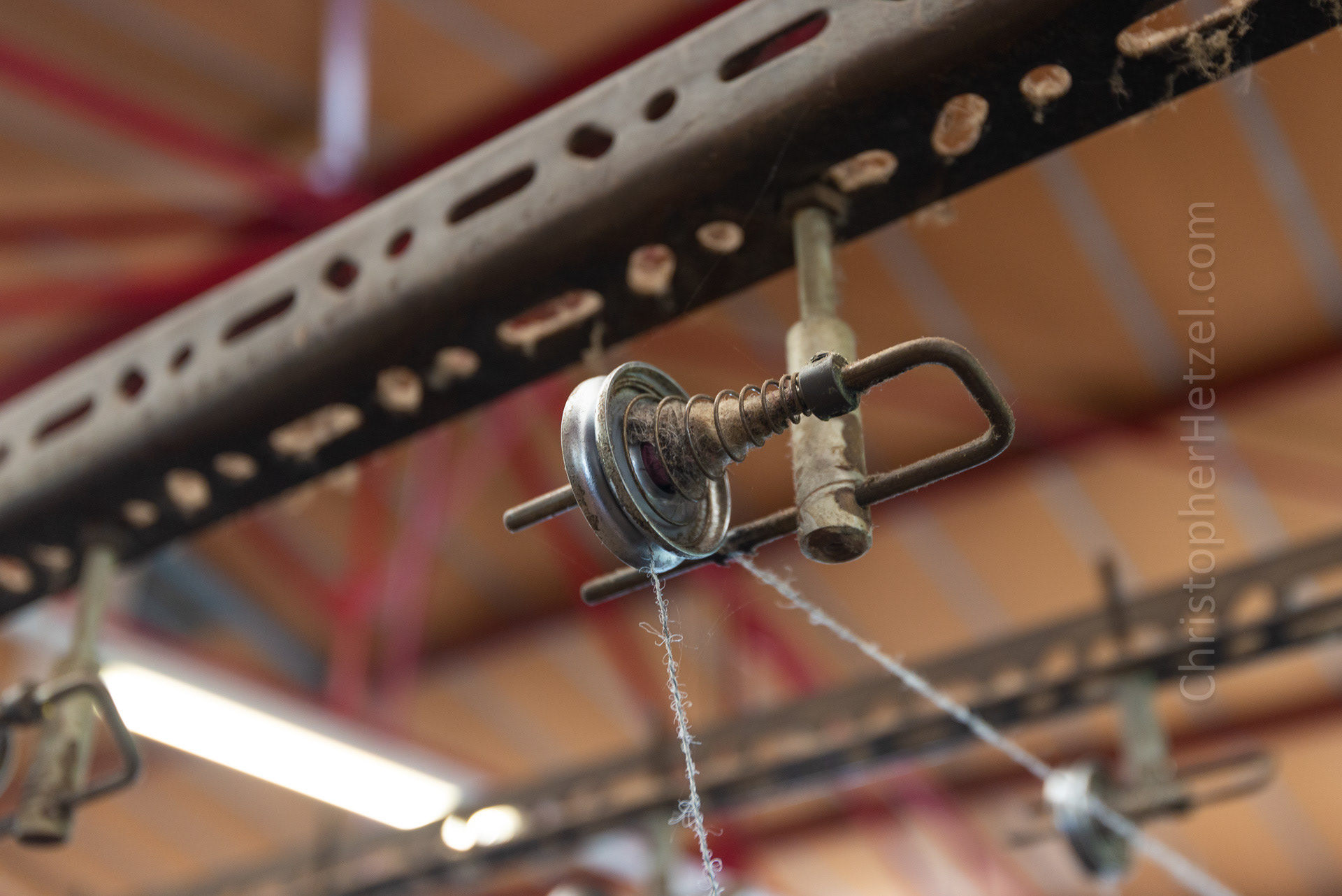
Hanking - The yarn is would from bobbins to 'hanks,' which is the form used to wash and dye the yarn.
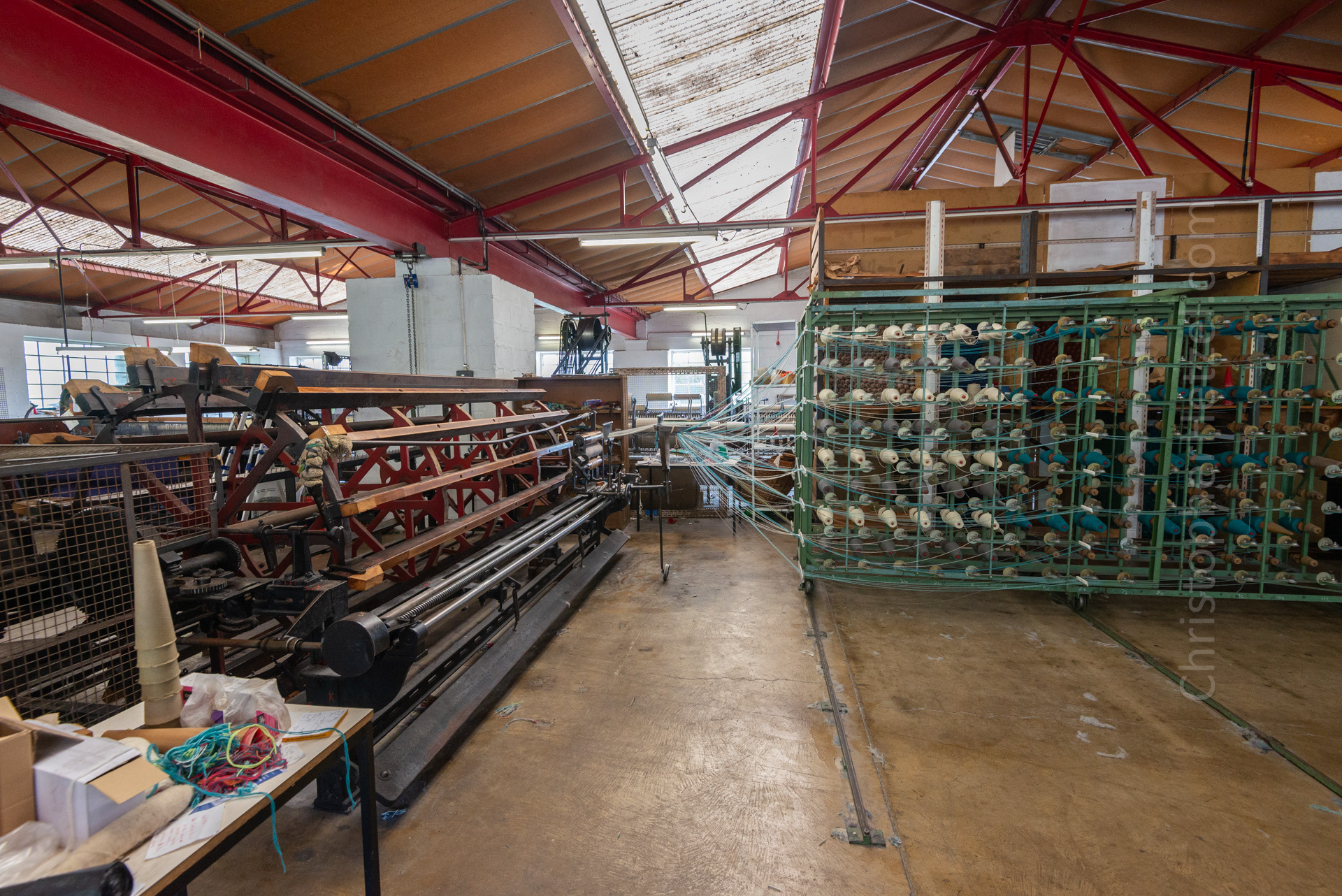
Warping - To prepare for weaving, threads of yarn are transferred from cones to bobbins, which fit into the shuttles of the weaving machines. Meanwhile, a warping machine arranges the threads to form the warp. This image shows the latter process.
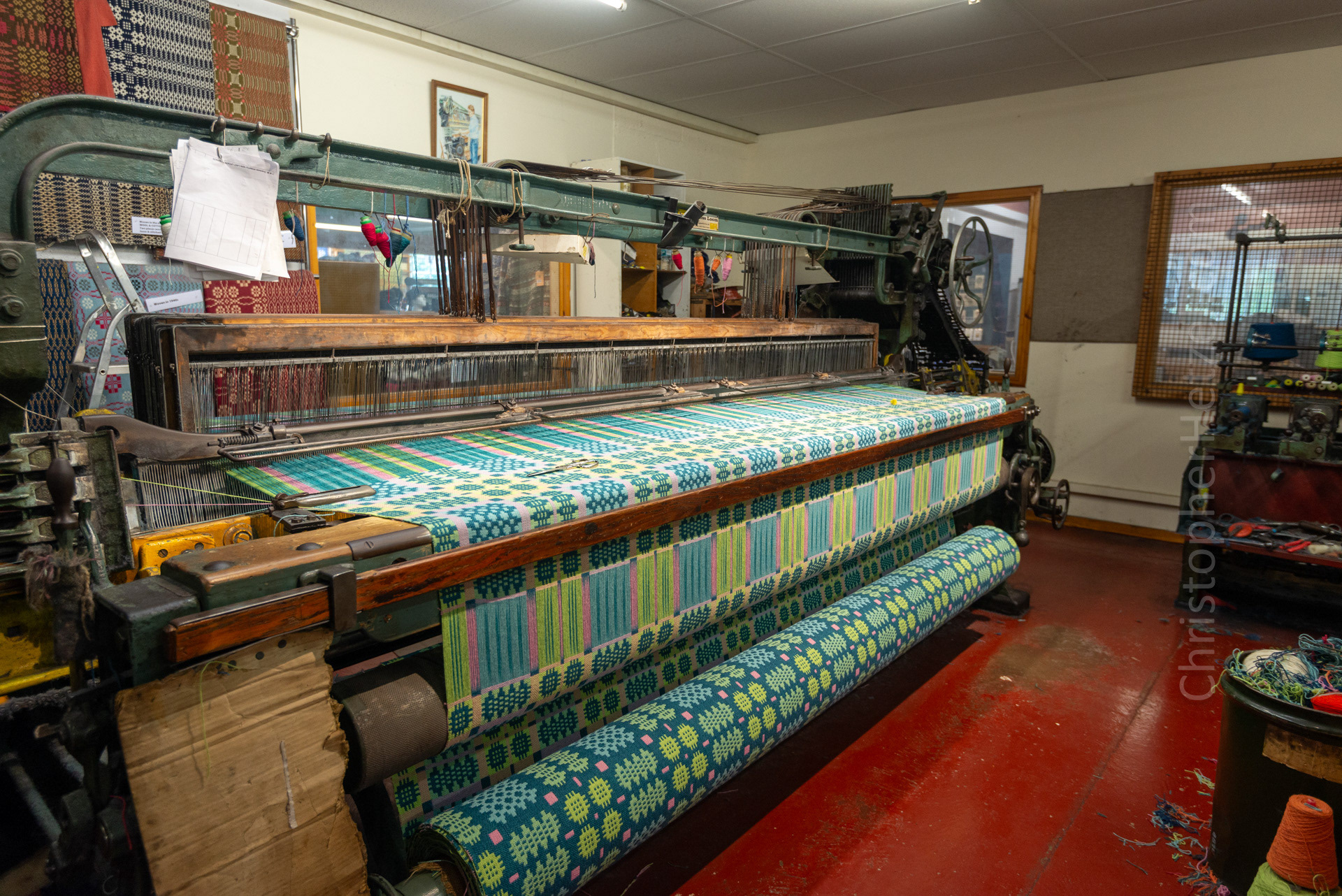
Weaving - The weaving of cloth is done by a loom, which utilizes as many as five shuttles to carry the weft thread horizontally across the vertical warp, while the shafts are raised and lowered to make the pattern.
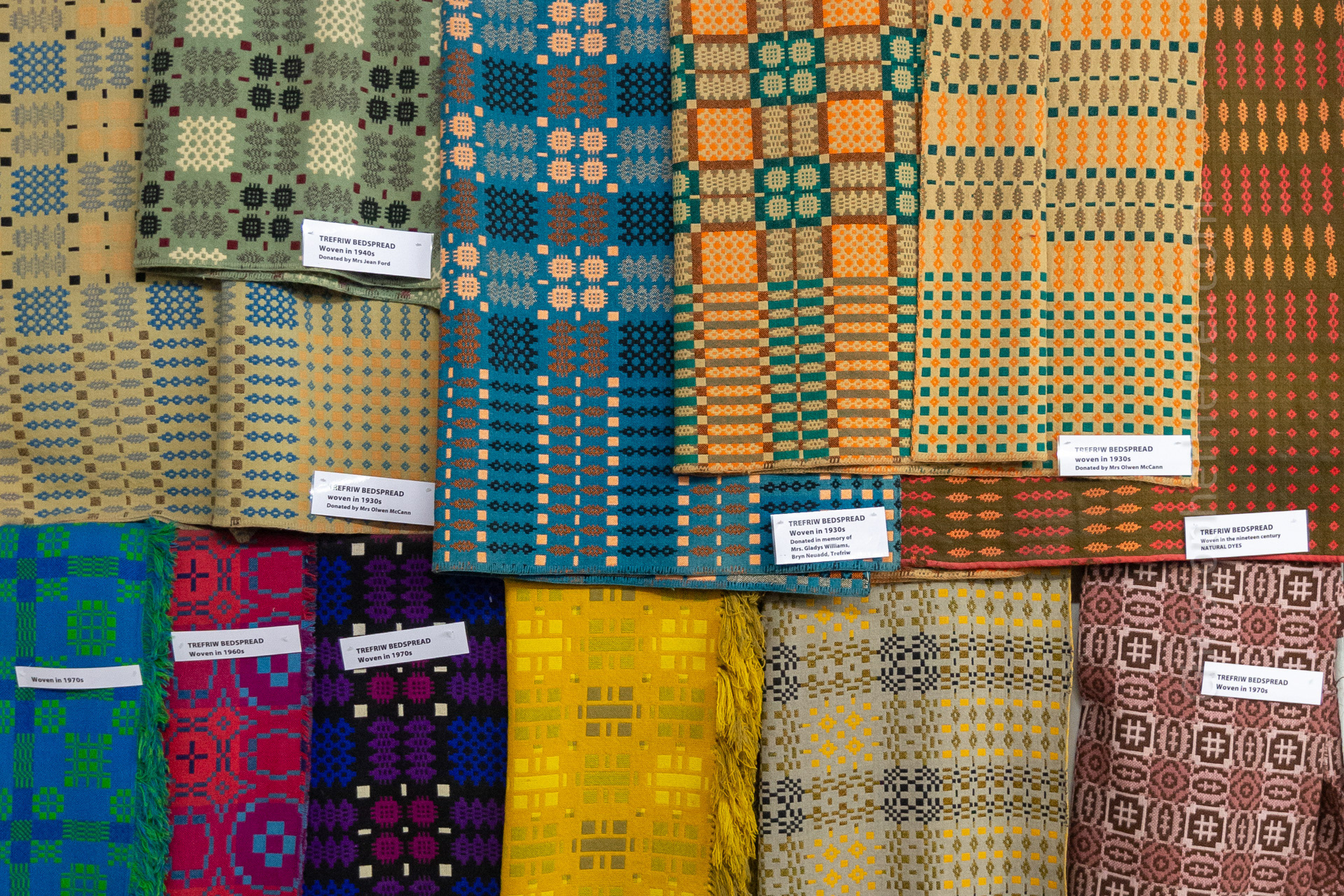
Fabrics from across the ages. The patterns are geometrical because the designs are shaft controlled. Each mill had its own signature pattern, and it's possible to identify the source of most wool fabrics as a result. Historically, there were hundreds of mills and, as people did not travel as much in the 19th century, textiles were typically produced and purchased locally, near where one lived. Most mills would have had a stall at the local weekly market.
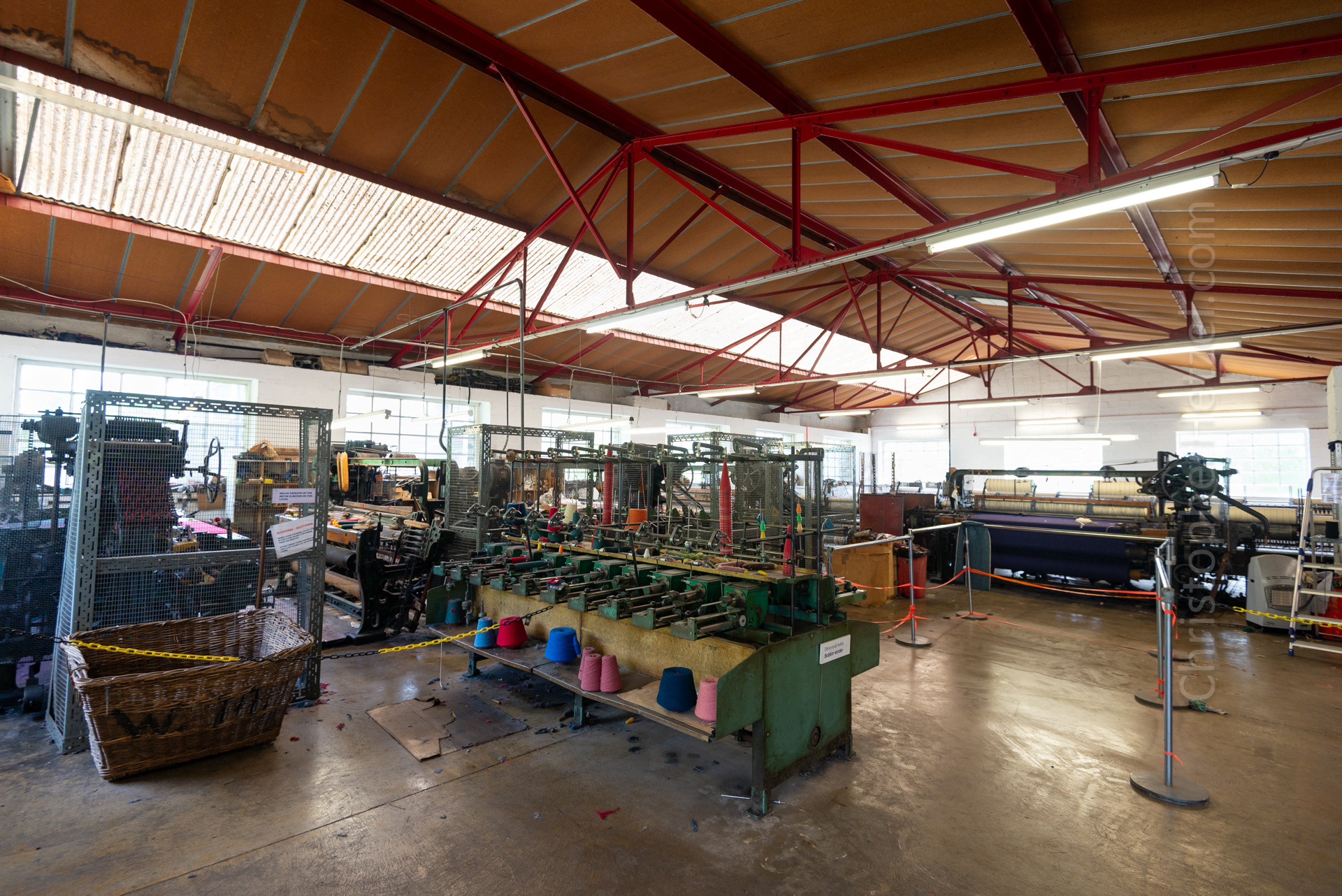
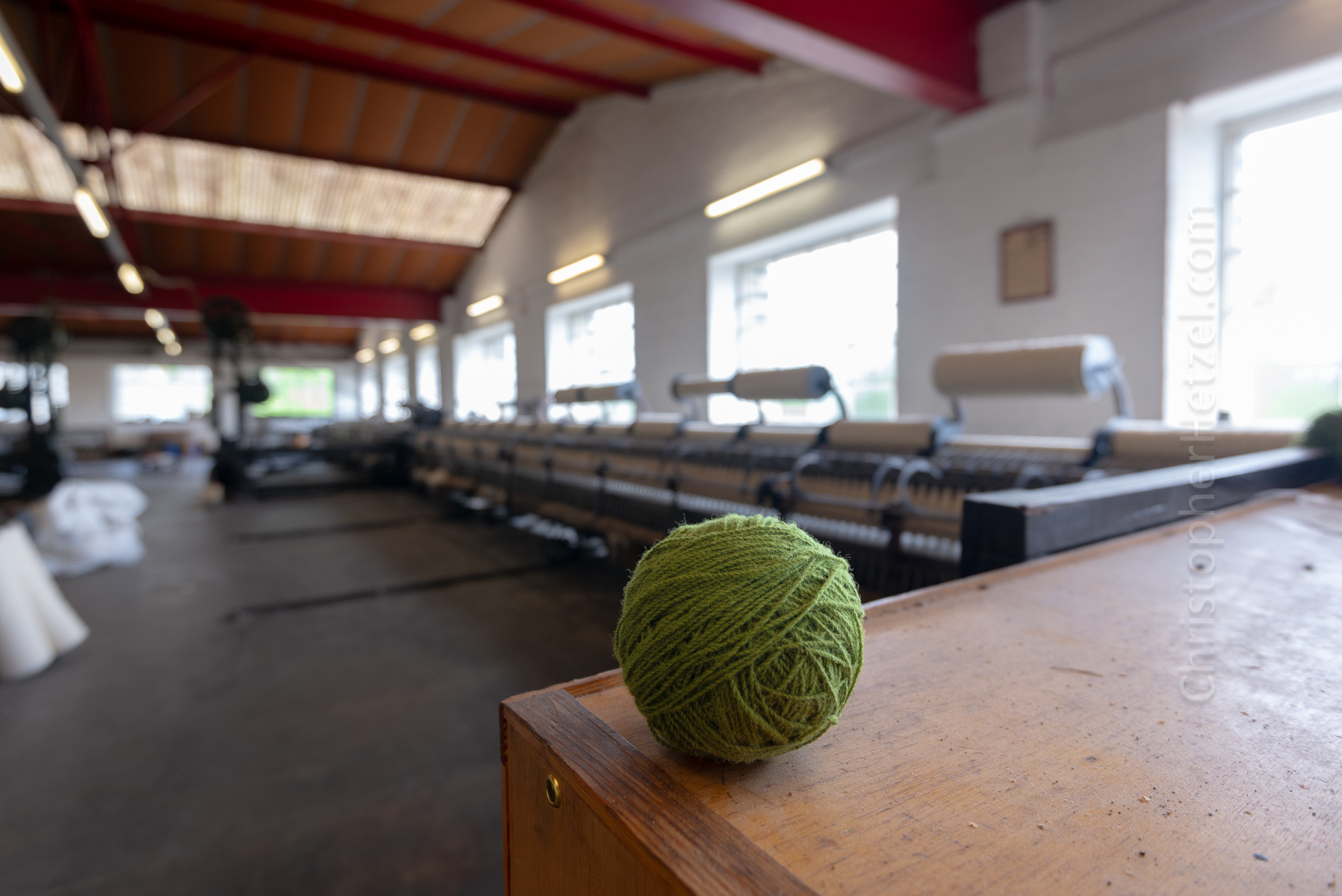
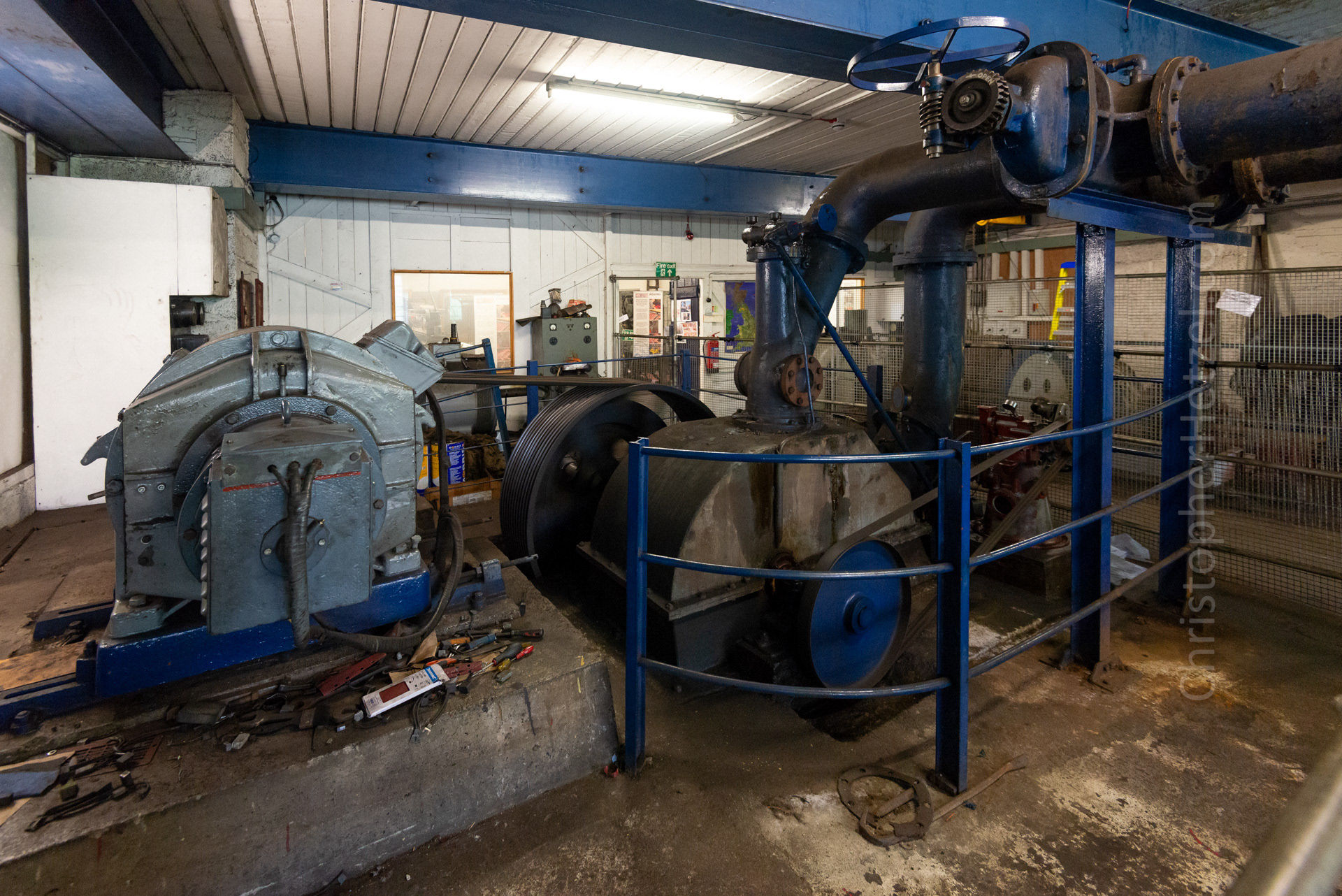
The turbine house. The River Craftnant is dammed about a half-mile upstream and the water diverted down a 20" diameter steel pipe to this location. It enters the turbine through the large pipe near the ceiling, and exits beneath in the concrete channel. Of the two turbines, only one generator is used at a time, as there is no synchronizing equipment. Water hits the buckets of the Pelton wheel contained in the circular compartment at a very high pressure, causing it to spin at great speed. A flywheel helps stabilize the speed of the machine, and a governor keeps the speed constant, by allowing more or less water to pass through at any time.
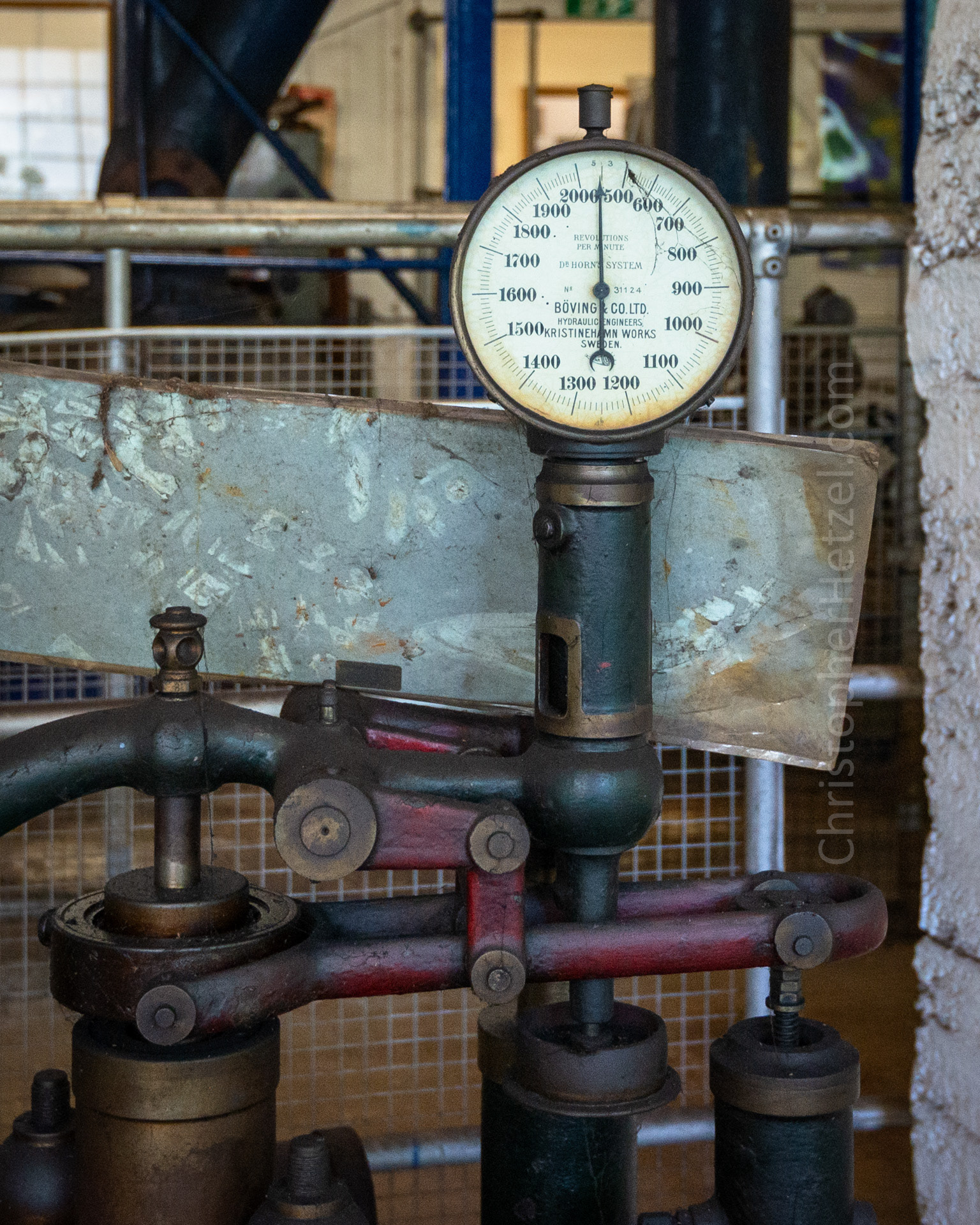
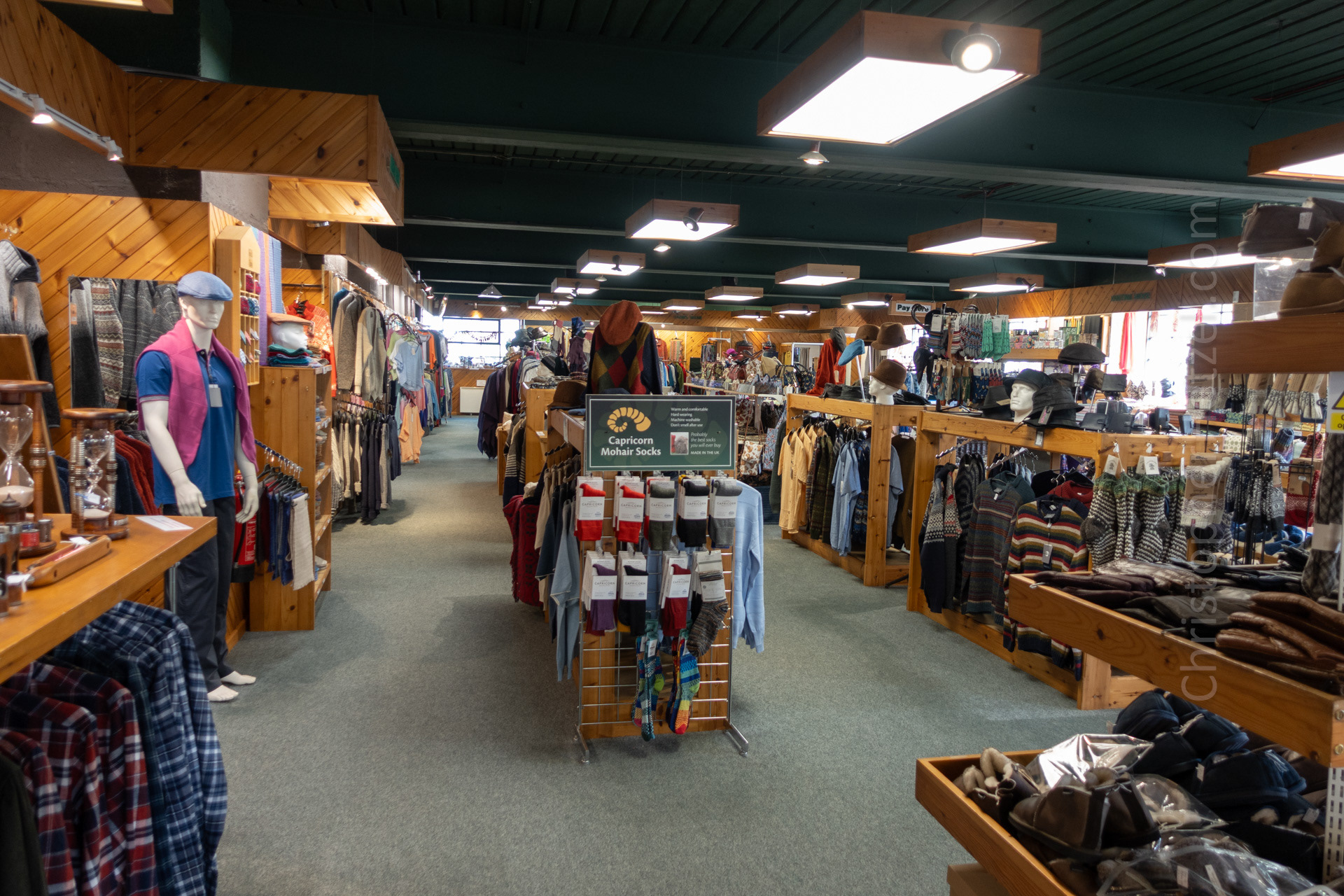
The mill's retail store!
Return to Wales